
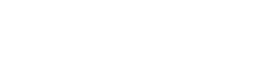
Babbini S.p.A. is historically known to anticipate times.
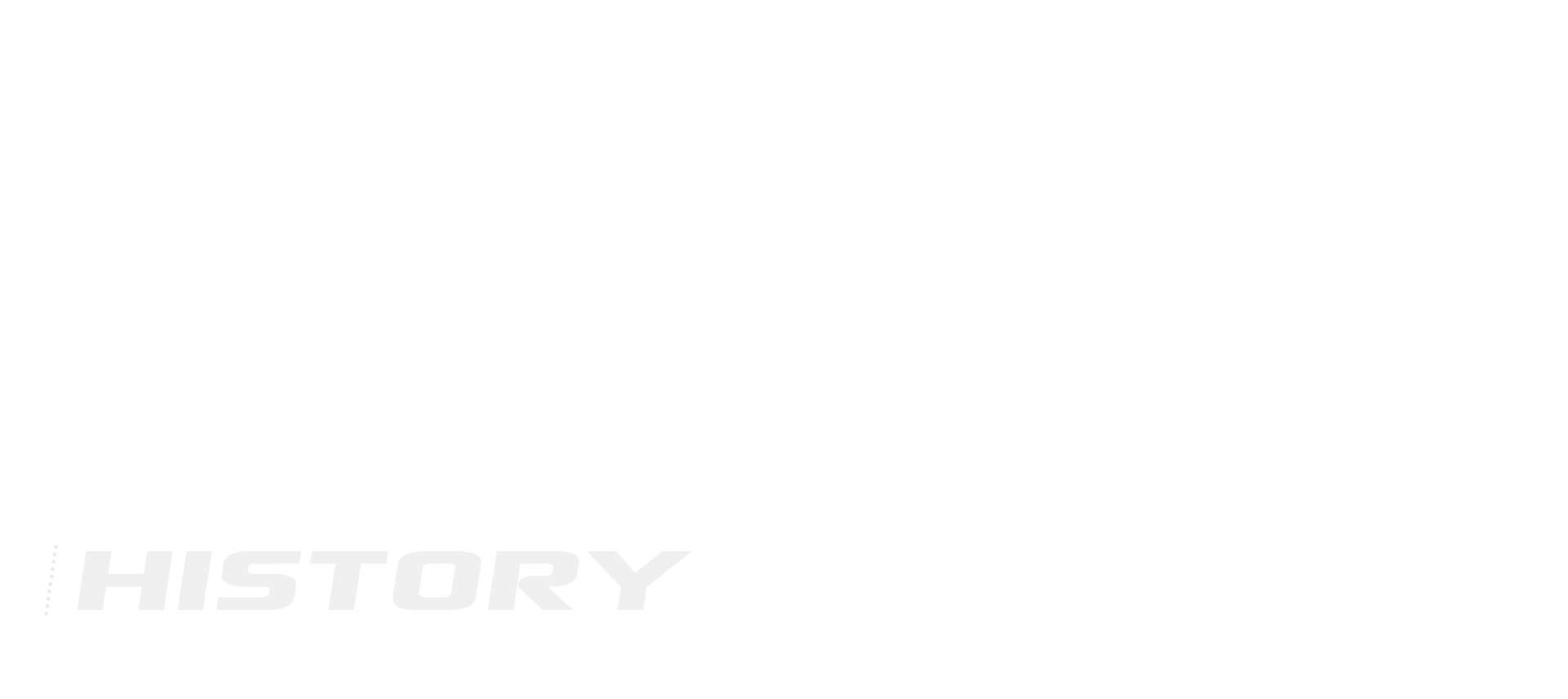
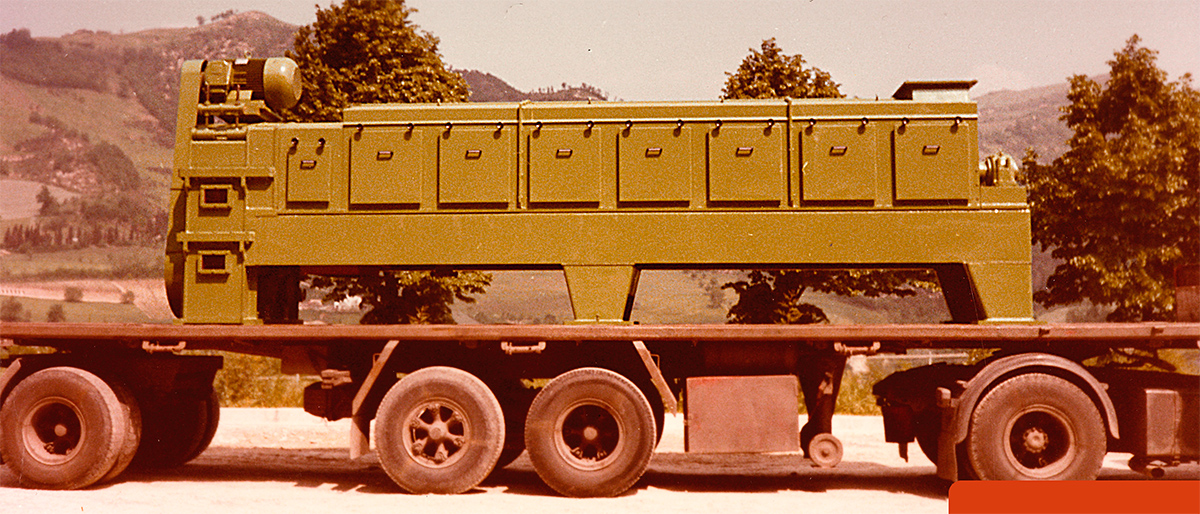
A HISTORY DEVELOPING IN PARALLEL WITH THE HISTORY OF DEWATERING BY MECHANICAL PRESSING
Babbini’s history counts 160 years of activity and since the mid 20th century it has developed in parallel with the history of dewatering by means of continuous mechanical pressing. The company has become an undisputed leader in this field, first in the Italian market and then also in the world market.
Starting from the 1970s it invested all its technical-manufacturing resources in the designing of continuous dewatering high-yield double screw presses, mainly intended for the sugar industry, thus meeting the needs for the several Italian sugar factories to rely on an Italian product as an alternative to the equipment by foreign monopolist manufacturers. Thanks to its patented features, Babbini developed an increasingly improved and exclusive products, completely manufactured at its premises (designing, manufacturing, test), quickly achieving its current leading position. Thanks to its experience, the success in the sugar industry was soon followed by the success in several other fields, like paper, agro-industrial, biomasses industries. In year 2018 during a celebrative party, the 1000th press was delivered (click here below to see some of the most important moments of this event): an important goal, that has now been well exceeded
Press with compact design gearbox – 1977
In 1977 Babbini proposed the first press equipped with a compact design gearbox.
BABBINI P24
Babbini P24 (dating back to 1982) is the first big size press on the international market.
“1000th Press” event
On occasion of the delivery of the 1000th manufactured press in May 2018, Babbini organised the “1000th press”.
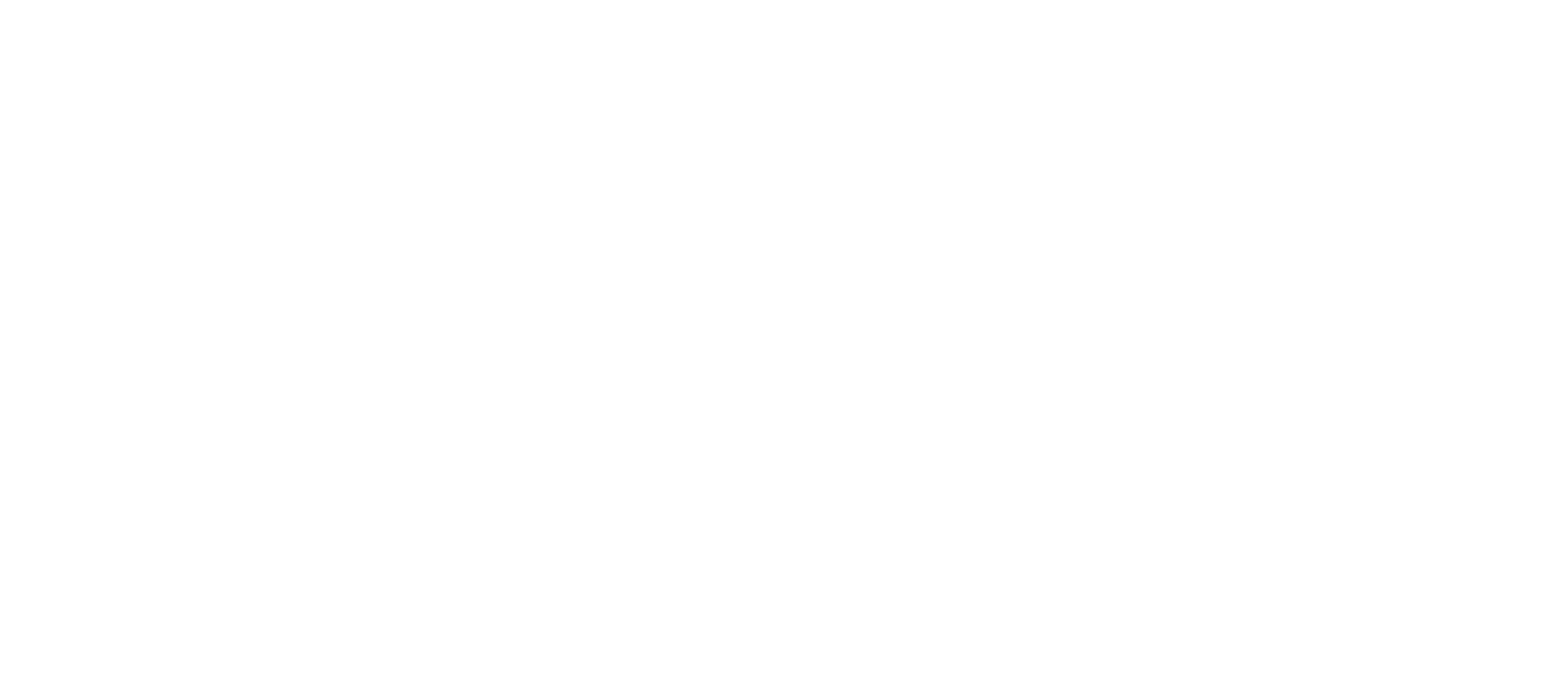
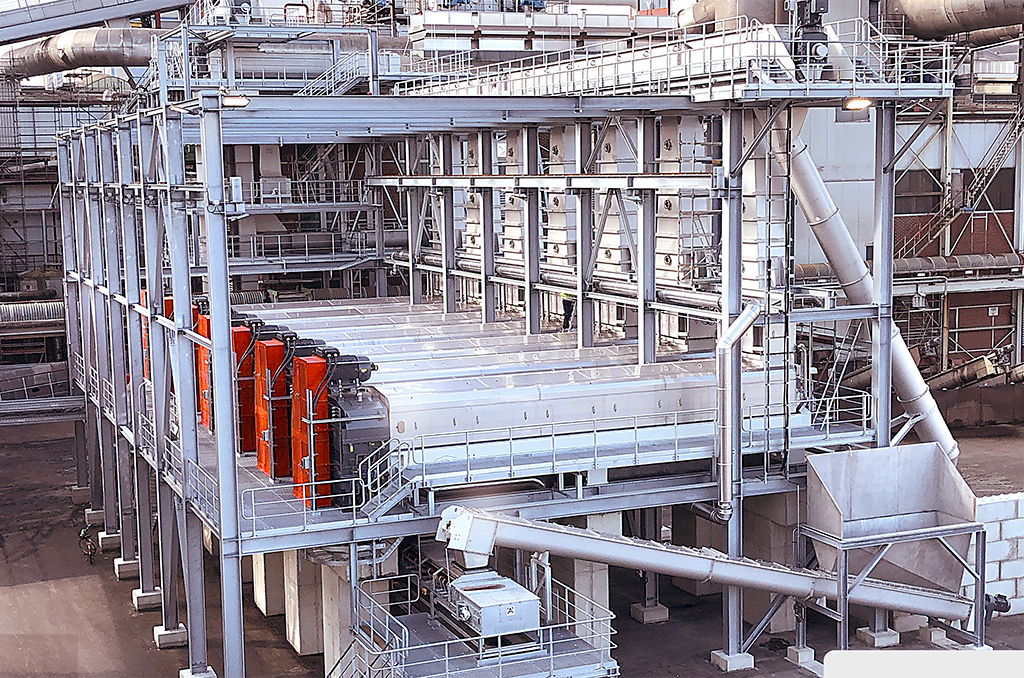
THE RESULT OF THE FARSIGHTED CHOICES OF THE PAST
Nowadays, Babbini is the result of its past farsighted choices. The company organisation chart has gradually included new engineers working along the historically established team, in the frame of a constant and innovative designing development. This assures a continuous product improvement from the point of view of reliability and pressing efficiency, thus leading to the constant increase of Babbini’s market share.
The customer can therefore take advantage of a solid and concrete historical background, constantly growing over time, and of a Made in Italy product, accurately studied in all its details.
An interesting curiosity: at the company reception you can see a painting representing the concept of Babbini’s view of its activity.
PB 48 FS/FSP and PB 22 F
Six Babbini PB 48 FS/FSP presses and one Babbini PB22F press are installed in Arcis-Sur-Aube, in one of the biggest sugar factories in the world.
PB 32 SP
Seven Babbini presses type PB 32 SP are installed near Nordstemmen in Lower Saxony (Germany).
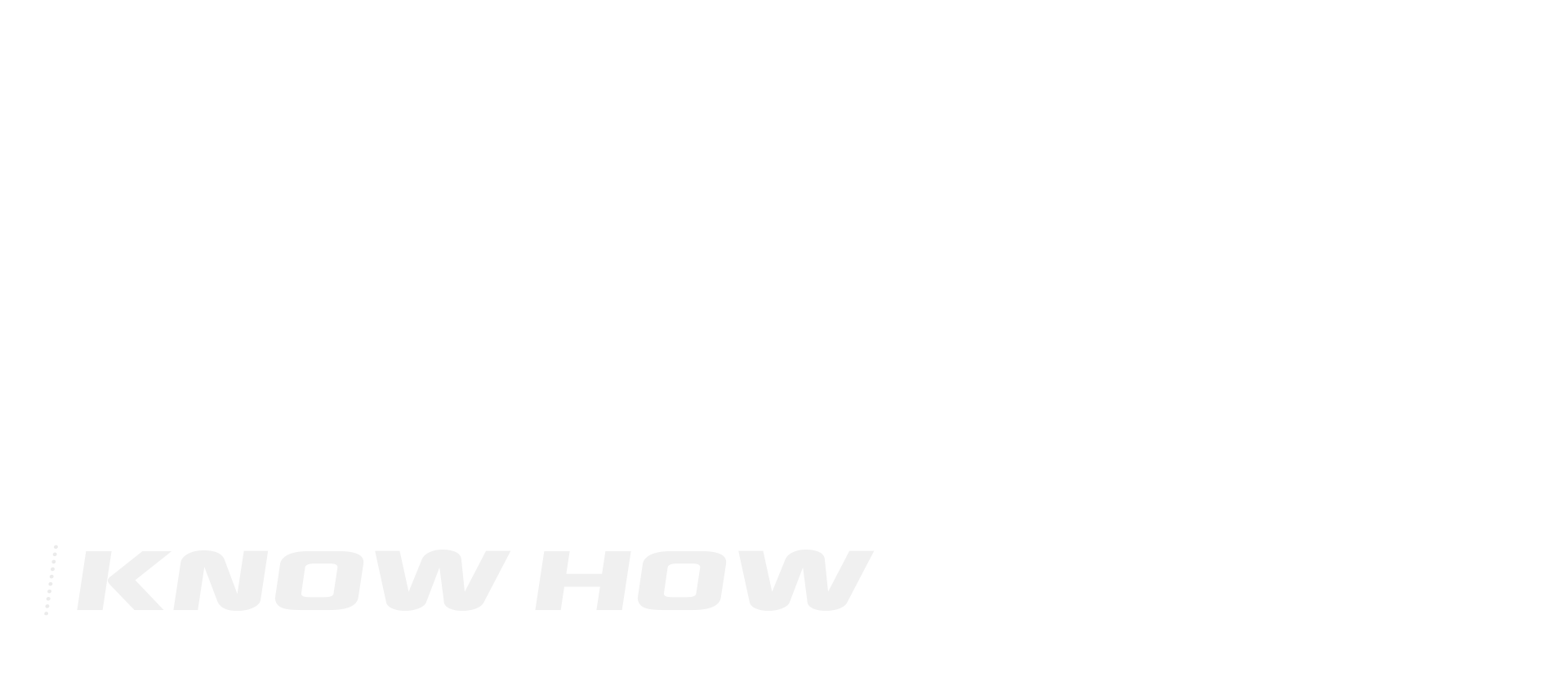
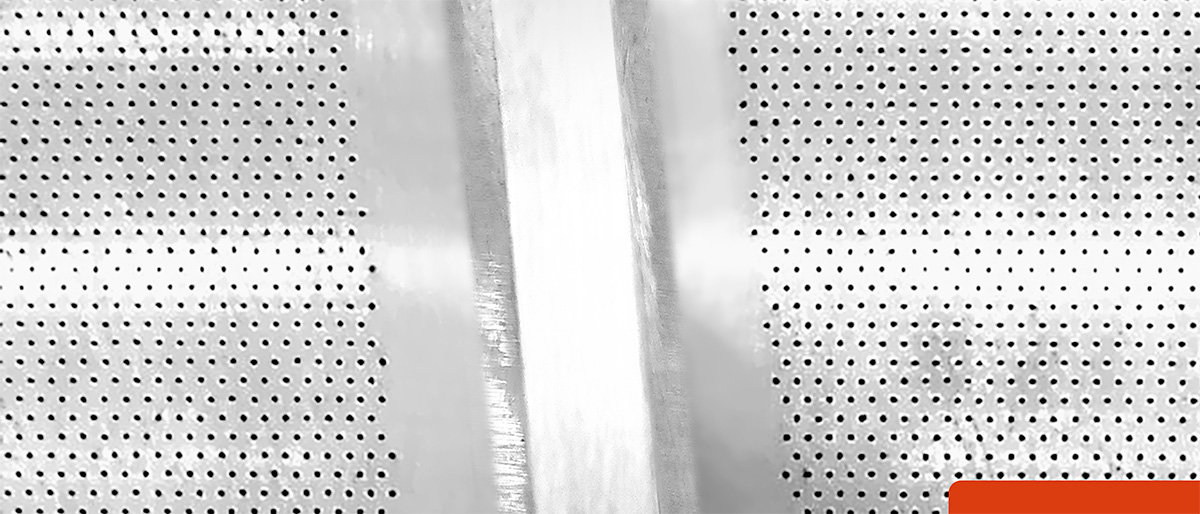
BEING AHEAD OF TIME IS THE PERMANENT MISSION OF BABBINI TECHNICAL MANAGEMENT
Continuous and constant research and development have always characterised Babbini, who has always been ahead of time, thus becoming an excellent performer in the field of pressing. Babbini is the only company in the world able to manufacture both vertical and horizontal double-screw presses, with a capacity going from 1000 to 6000 t of beets/day. Here are its main peculiar features, making up our constantly improving technical background:
•Presses covered by several patents, allowing both to improve their performances and mechanical reliability and to reduce their power consumption, making them more efficient;
•Cooperation with important research institutes to arrange the most appropriate manufacturing cycles;
•Setting up of workgroups for research and development on pressing in cooperation with customers;
•Availability of pilot presses to test new products and for a continuous research on pressing.
Babbini does not outsource its production department. The management of all the manufacturing cycle takes place inside its premises, thus assuring an accurate control over every single detail.
Babbini has got quality certification since 1996. From 2002 it complies with the ISO 9001:2008 regulations.
Draining spindles with unperforated bands
This patent concerns the flights welding made on an unperforated helical band located in the spindles perforated plates. It is an absolutely innovative execution allowing to take advantage of the higher draining efficiency of a press equipped with these special perforated spindles, i.e. a higher DS% content in the pressed product in presses having the same dimensions and capacity, while assuring their utmost mechanical reliability.
Single screw presses for paper mill wastes
The single screw presses type MIC6, first manufactured in 2015, have progressively established on the Italian market thanks to their performances and reliability. The references in this field include the most important Italian companies, as well as several multinational corporations that took Babbini presses beyond the Italian borders: a natural course of the product diversification that Babbini has been implementing in the last few years.
Double screw presses for paper mill wastes
The product diversification that characterised the single screw presses also involved the use of double screw presses in paper mills, that represented an actual and successful revolution in this field.
After a thorough research and trial stage based on Babbini experience in the sugar and agro-industrial field, the huge advantage brought about by this technology in the fibrous wastes treatment was evident, as efficiency turned out to be almost double compared to the traditionally used machines.
Thanks to its knowledge in the agro-industrial field, as well as on the its experience with the MIC 6 presses automation, Babbini was able to design a series of presses especially intended for installation in paper mills.
Some photos of Babbini company, its premises and products
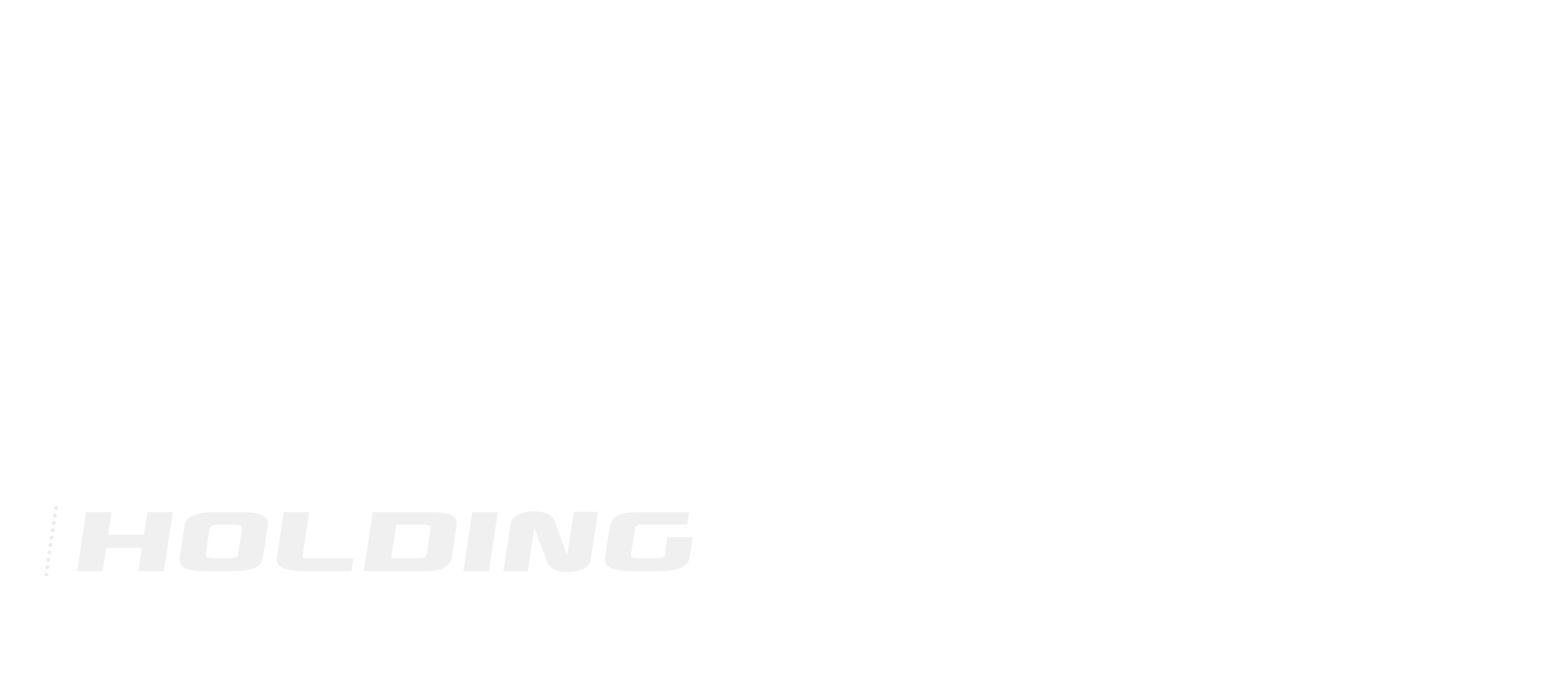
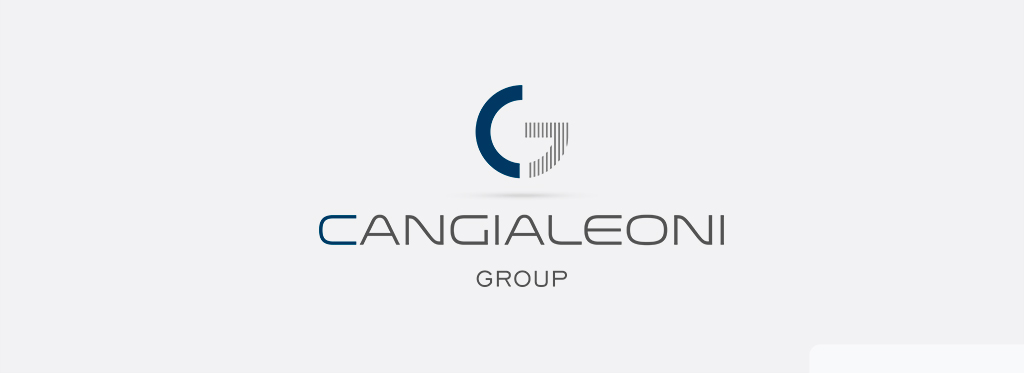
BABBINI IS AN INTEGRAL PART OF THE CANGIALEONI GROUP
Babbini S.p.A. has been part of the Cangialeoni Group since 2001, a solid holding operating in the field of the Italian and international metalworking industry. Among other companies, the group also includes GPS Engineering, a company located in the Milan area that also manufactures the gearboxes equipping all Babbini presses.
This special synergy allows the customer to have a highly customised high-quality product, and to rely on the availability of spare parts as well as on a 24/24h 360° service.