
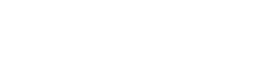
The patents and exclusive features that made our international success
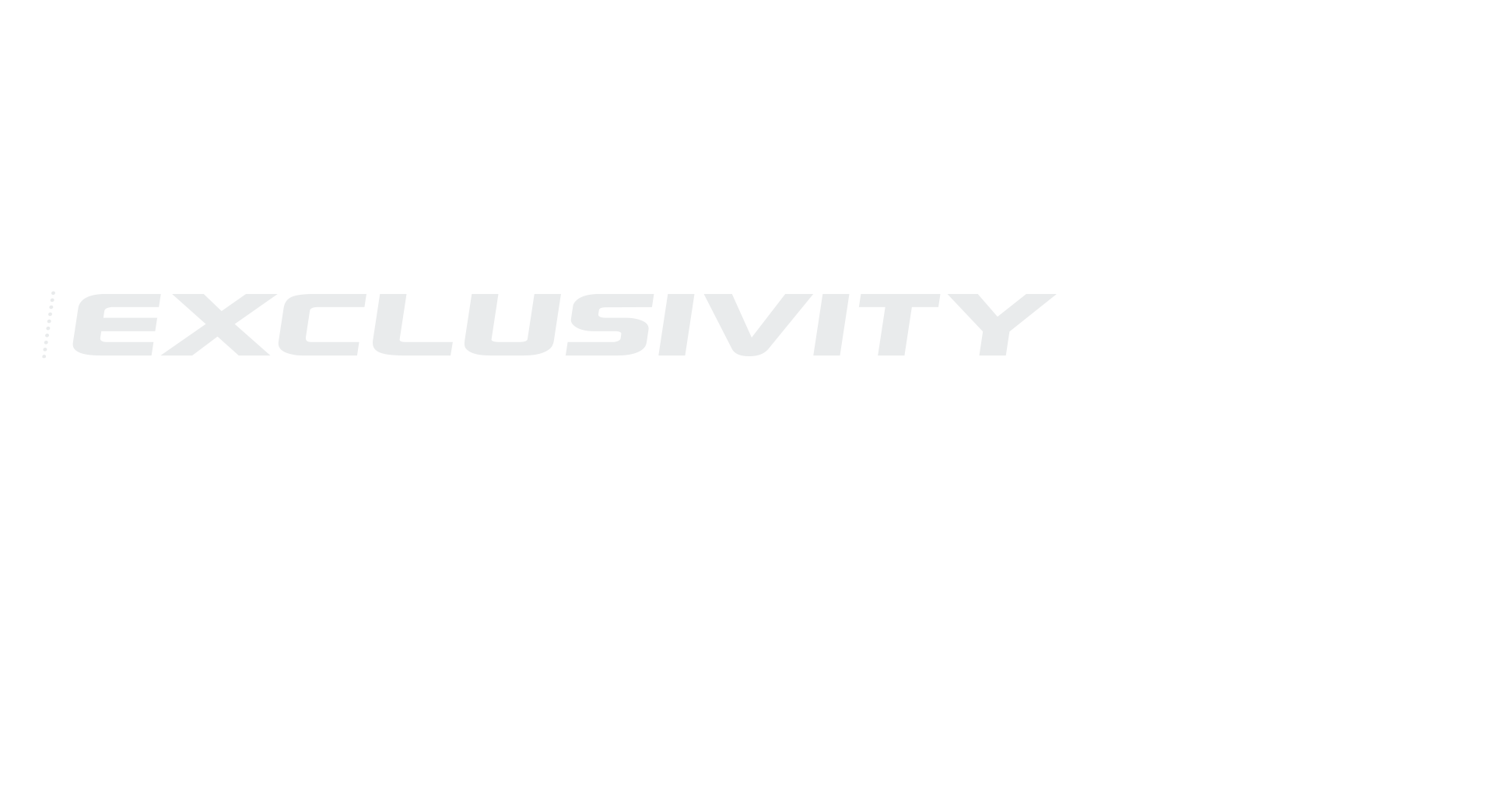
THE REASONS OF BABBINI’S SUCCESS
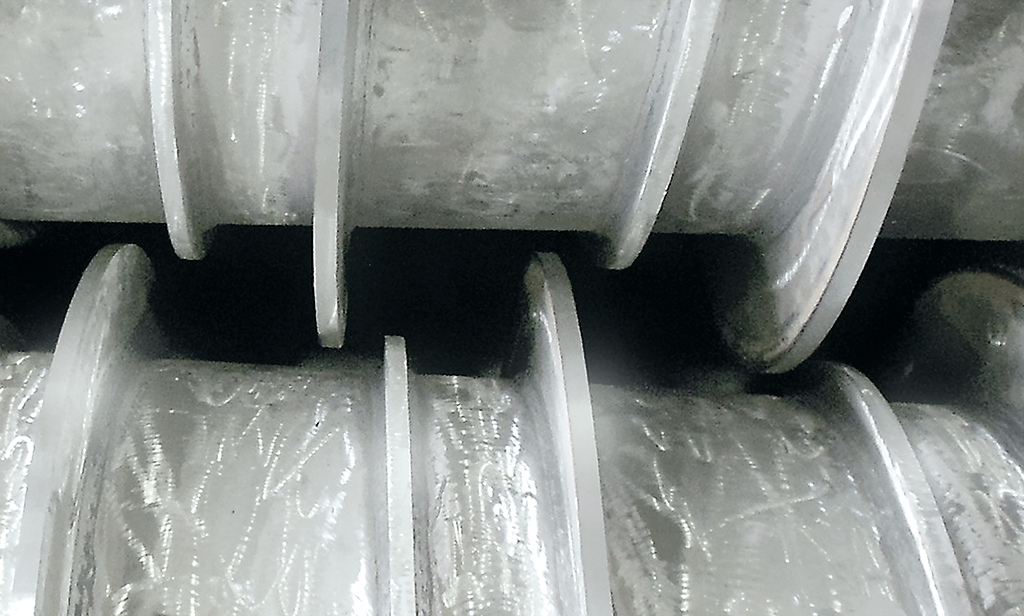
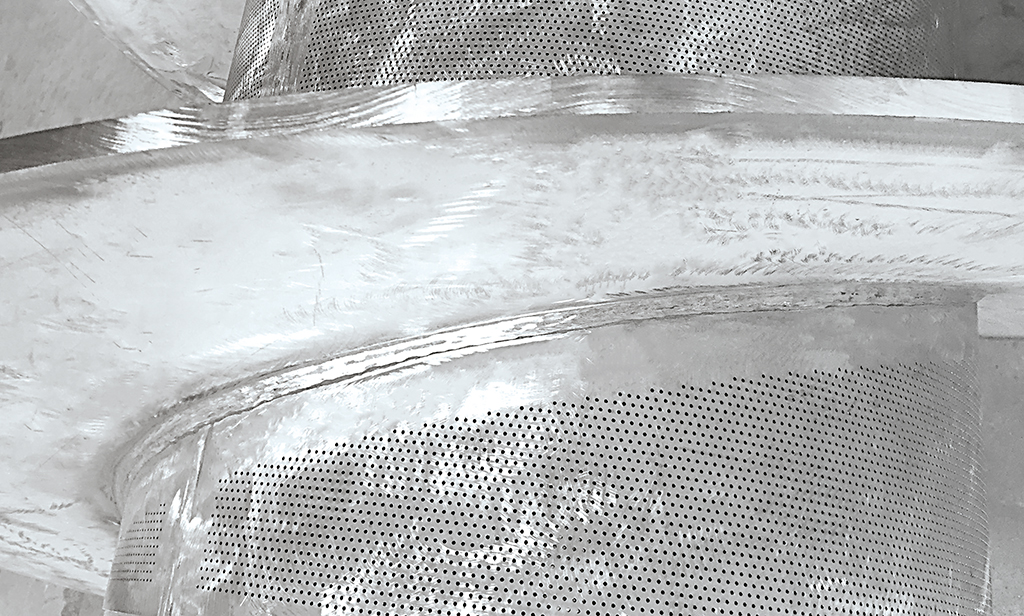
Babbini presses are covered by several international patents increasing their performances and mechanical reliability while reducing their power consumption, thus improving their efficiency.
Their technical characteristics make them substantially different from the other presses on the market, and they are more performing from any point of view.
Every historical patented innovation in the field of beet pulp pressing is a result of Babbini’s research, that has become a common heritage after the expiration of the exclusive right.
Summarising, the main patents assure:
- ↑ Higher product reliability and quality (both with self-draining and unperforated spindles)
- ↑ Increase in performances
- ↓ Lower power consumption
In addition to the advantages brought about by the above mentioned patents, Babbini can also rely on its advanced management modes, including the insourcing of all manufacturing, assembly and testing processes and the installation of specially designed gearboxes, manufactured by the sister company GPS Engineering.
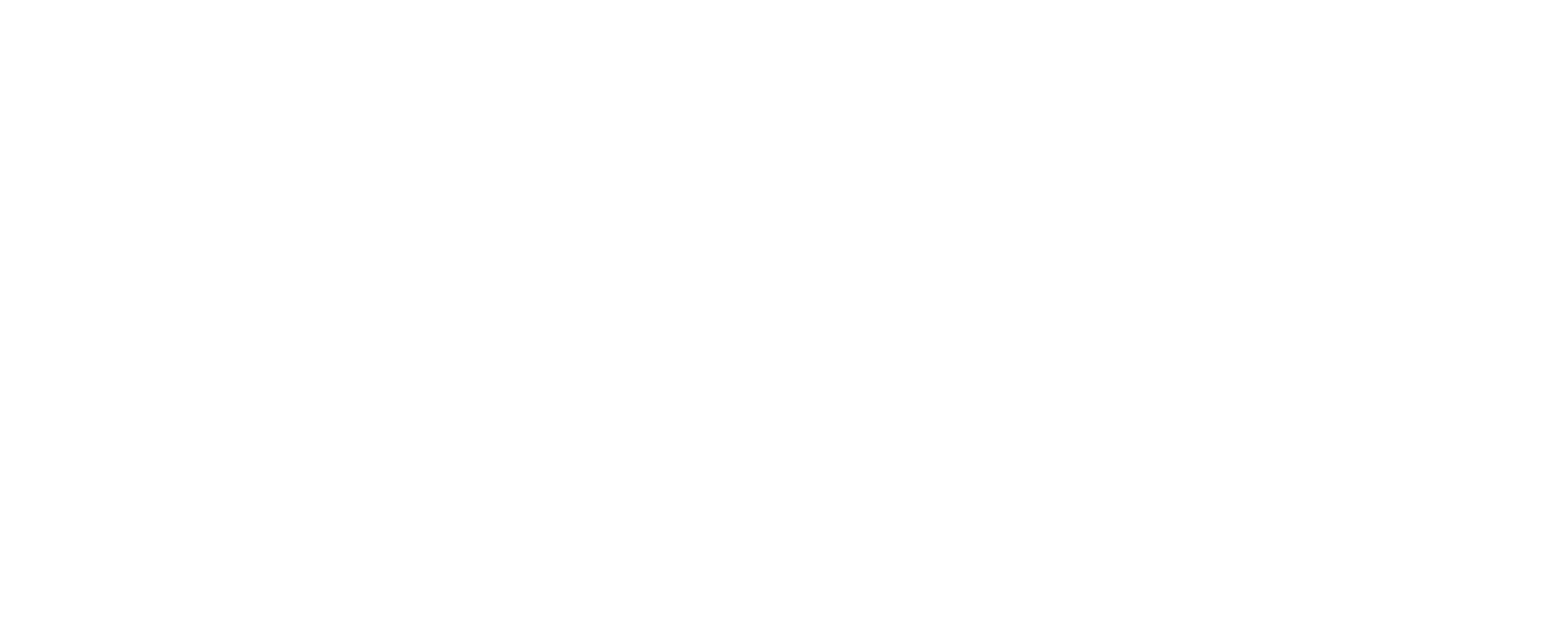
EVERY PATENT IS A MILESTONE IN THE SCREW MECHANICAL PRESSING
1 – BICONICAL PRESS (1988)
All Babbini presses are now manufactured with biconical geometry, i.e. with conical shaft, screw and draining cage. Thanks to this patent Babbini modernised pulp presses since its entry into this field, as it assures higher performances compared to the now outdated bicylindrical shaft geometry.
Indeed, this patent allows the material to move forward more constantly and uniformly than in the old generation (bicylindrical) presses, so the press can grant higher capacity and DS% with a lower power consumption.
2 – SPINDLES SHAFT MADE UP OF BEAMS (1988)
The spindles of Babbini presses are made up of beams. This makes the spindles more sturdy and reliable also under high stress, thus allowing the press to achieve higher performances.
3 – SECOND FLIGHT (1996)
The addition of a second flight in part of the spindle allows to improve and optimise the pulp motion forward, thus increasing the press performances and reducing the power consumption.
4 – WIDENED FILTERING SURFACE (1999)
Widened spindles filtering surface to increase dewatering and therefore to improve the press performances.
5 – VERTICAL PRESS (2006)
Manufacturing of a vertically designed press with two counter rotating spindles.
The only manufacturer in the world.
6 – PULP REMIXING SYSTEM (2008)
This recently patented feature allows to furtherly increase the water draining from the exhausted pulp. The relevant improvement is brought about by pulp remixing, that is considered a fourth factor in addition to the ones that are commonly taken into consideration in pressing analysis, i.e. pressure, retention time and filtering surface.
This feature increases the pulp remixing naturally taking place inside the press, favouring water draining from wet pulp, and consequently increases the final DS% in the pressed pulp.
7 – DRAINING SPINDLES WITH UNPERFORATED BANDS (2018)
This is an innovative manufacturing feature allowing an absolutely reliable exploitation of the economical advantages of draining spindles compared to the traditional unperforated spindles.
The innovative design of perforated plates with unperforated bands, allowing to weld the flights on an unperforated helical band. This combines the higher performances of a press equipped with draining spindles and the mechanical reliability of a press equipped with unperforated spindles in one single product, as it eliminates the causes of the failures occurring on perforated spindles next to the welding at the flight basis.
See also The industrialisation process begins – P50V-A in the “News” section.
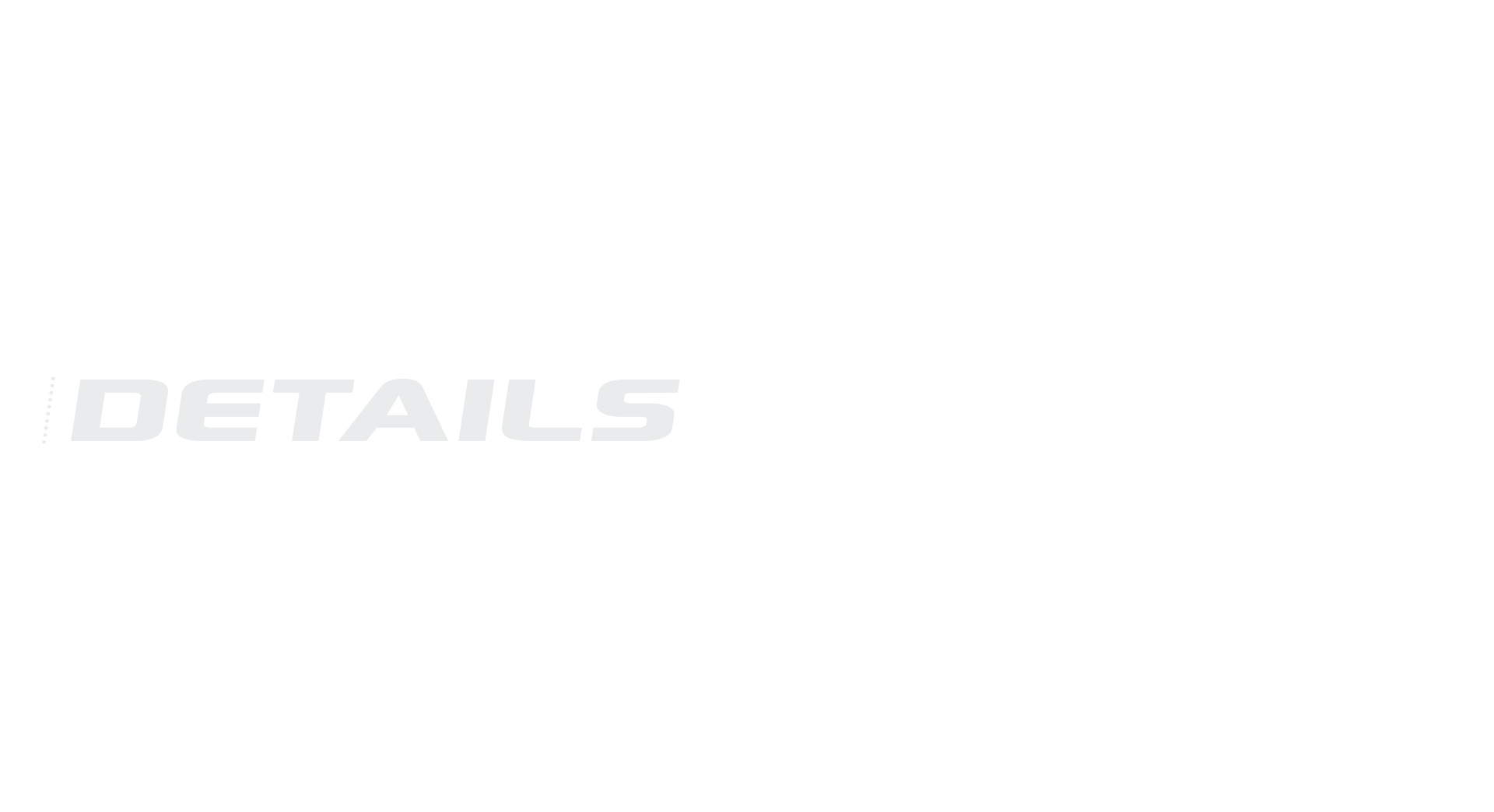
COMPLETE PRE-ASSEMBLY AND TEST
All presses manufactured by Babbini are pre-assembled and accurately tested inside Babbini workshop, in order to assure an easy on-site installation, free of any inconveniences, and to make an optimum press setting before its delivery to the customer.
Apart from preventing any inconvenience during the installation at the customer’s premises, it also makes this operation much faster.
“GPS ENGINEERING” GEARBOXES – THE ACTIVE COOPERATION BETWEEN TWO SISTER COMPANIES
All the gearboxes equipping Babbini presses, are designed and manufactured by GPS Engineering S.r.l. (a photo of its warehouse). This company is an integral part of Cangialeoni Group, like Babbini.
The close cooperation between Babbini and GPS gives the possibility to grant the customers some advantages, that could be impossible in case presses were equipped with the standard gearboxes that can be found on the market. Here the most important ones:
• customised manufacturing of all special gearboxes, also in uprated version, to meet the needs of every single manufactured press;
• 24/24h service also on gearboxes;
• availability from the stock of all spare parts for gearboxes (in addition to the spare parts for the presses);
• customisation of gearboxes with special devices – such as the external oil filtration unit – upon customer’s request and needs (see the second photo);
• special device for vibration detection and other options to increase safety both for the press and the gearbox.